Transforming Tribology With AI
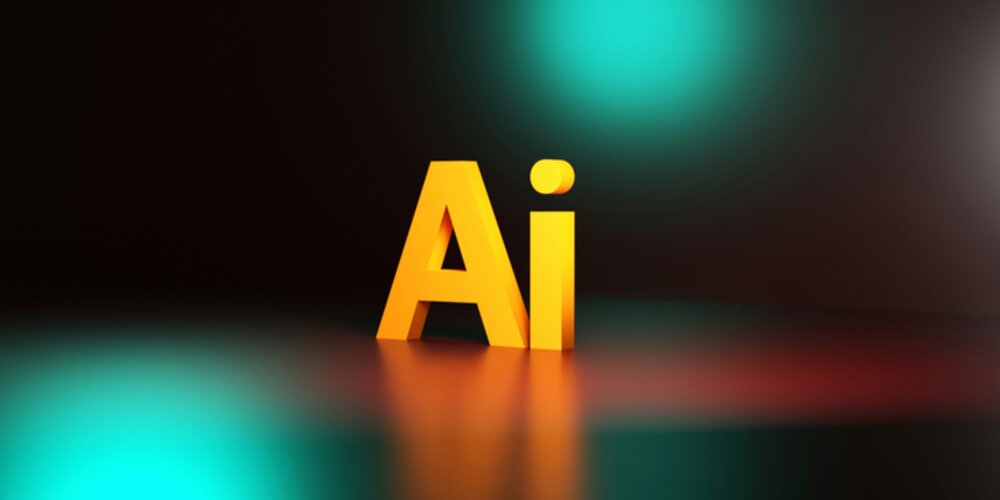
Artificial intelligence (AI) is revolutionising the tribology world by providing powerful tools to analyse complex data and predict system behaviours.
With its remarkable learning capabilities and rapid processing speeds at its disposal, AI offers a significant boon to researchers by being able to swiftly identify valuable patterns, trends, and associations within complex data.
This is of particular interest to the study of tribology, which utilises system-dependent behaviours that evolve over time, and occur at multiple levels and scales. The integration of AI in tribology is not only advantageous, but also crucial for enhancing the understanding and fostering innovation within this diverse field.
AI’s robust capabilities in data and pattern recognition can identify correlations between various signals - such as vibration, acoustics, electrical, and sound pressure - and wear, enabling the early detection of mechanical wear. It can also simulate and predict tribological behaviours under a range of operational conditions.
The application of AI technology in tribology can be divided into three main areas: explaining tribological behaviour mechanisms, advancing micro- and nano-tribology, and analysing behaviour patterns based on standard tribological experiments.
It is important to note that AI’s primary role is to establish data associations among different categories of information, rather than directly explaining mechanisms. To increase the effectiveness of AI in the fundamental theory of tribology, integrating physical models can improve the interpretability of AI’s computational results.
Intelligent tribology represents the importance of AI application in tribology research and is the field most impacted by AI advancements. It focuses on evaluating operational reliability and predicting the lifespan of tribological systems in critical engineering sectors such as transportation equipment, energy systems, and mechanical processing.
As technology has progressed, this field has expanded to include intelligent lubrication and friction material design. Thus, intelligent tribology can be categorised into two main areas: status monitoring, fault diagnosis, and life prediction of tribological systems, and intelligent lubrication and friction material design.
The fundamental components of tribology include elements that contain the core elements of a tribological system and perform key tribological functions within mechanical systems.
These components primarily consist of bearings, gears, tyres, fasteners, and seals. Bearings, in particular, are among the most complex and widely used components in tribology, and AI technology is extensively applied in bearing research.
The arrival of extreme service environments such as deep sea, polar regions, deep space, and deep underground presents unique challenges for tribological systems. The conditions found in these environments often lead to severe friction and wear, generating various intense derivative signals, which complicates friction and wear testing, online monitoring, and fault diagnosis.
However, the integration of AI technology offers new and more effective solutions to these challenges. AI’s role in extreme tribology is substantial, though the reliability of the data relies heavily on its quantity and authenticity. Obtaining accurate tribology information is a significant challenge in this field.
By utilising AI, extreme tribology can establish correlations between simulated environmental data and real working conditions, helping to bridge the gap between theoretical and practical data.
The integration of AI in tribology is a significant leap forward for the field, allowing for more accurate predictions, enhanced understanding, and innovative solutions to complex problems.
Manufacturing engineering services with Neale Consulting Engineers
The global manufacturing industry is vast, spanning everything from industrial processes like steel production to everyday household consumables.
Implementing engineering and tribological best practices in your maintenance schedules can significantly benefit your manufacturing business.
If you want to discover the benefits of engineering best practice for your manufacturing business, contact our team today.
Contact Neale Consulting Engineers today
- Date
- 15/05/2025