The Macro and Nano-Tribology of Carbon Nanotubes
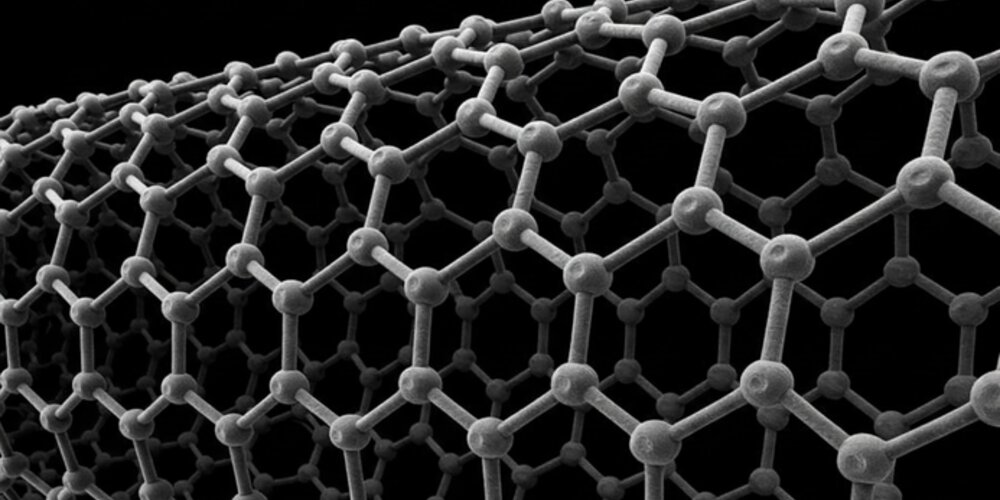
Carbon nanotubes are reshaping the understanding of friction and wear at both macroscopic and nanoscopic levels.
Since their discovery in 1991, carbon nanotubes (CNTs) have captivated scientists with their unique properties, including high aspect ratio, extraordinary mechanical strength, exceptional thermal conductivity, and remarkably low density.
These nanomaterials have improved the tribological performance of various systems, thanks to their ability to reduce friction, repair worn surfaces, and form protective tribofilms.
At the macroscale, CNT-reinforced composite coatings, bulk materials, and lubricants have become the focal point of extensive research. Their ability to act as nano-roller bearings or to fill in and restore damaged surfaces demonstrates a remarkable capacity to reduce friction and wear under stress.
The ‘self-lubricating’ behaviour of CNTs enhances the durability of materials by forming protective tribofilms that can achieve near-zero friction, a state referred to as superlubricity.
Yet, this potential is not universally realised. Compatibility and uniform dispersion of CNTs within solid or liquid matrices are critical factors. Scientists have emphasised the importance of substrate selection and precise modifications of CNTs, along with optimising their concentration and orientation.
At the nanoscale, CNTs have been extensively studied through advanced techniques such as atomic force microscopy and friction force microscopy. These experimental investigations reveal a fascinating anisotropy in CNT frictional properties.
The frictional behaviour of CNTs varies depending on whether the sliding occurs parallel or perpendicular to the tube's axis. When sliding along the longitudinal axis, friction is significantly lower due to smoother movement facilitated by longitudinal dimples. Transverse sliding causes the tubes to deform and oscillate, dissipating more energy and thereby increasing friction.
However, the presence of structural defects and functional groups adds another element. While defects typically elevate intrinsic friction, they can also improve fracture toughness in composites by strengthening interfacial resistance.
Researchers are actively exploring ways to manipulate these properties, turning potential weaknesses into strengths for tailored applications.
In recent years, vertically aligned multi-walled carbon nanotube (VACNT) films and arrays have gained attention for their impressive tribological performance. Experiments have shown that treating CNT surfaces with CF4-plasma can reduce friction coefficients by half due to diminished surface energy, which weakens adhesion forces.
Aluminium-coated VACNT surfaces demonstrated a dramatic 79% reduction in friction coefficients, thanks to increased lateral stiffness that minimised contact area.
From enhancing the wear resistance of mechanical systems to enabling the next generation of nanotechnological devices, CNTs may yet redefine the boundaries of tribology.
Failure analysis with Neale Consulting Engineers
Physical damage of a machine, whether caused by incorrect design or installation, improper use or friction and wear have an enormous cost to industries of all types.
At Neale Consulting Engineers, we offer an engineering and mechanical failure analysis service to determine how and why a failure has occurred, and aim to provide recommendations and actions to prevent the recurrence of any issues.
Contact our team to learn more about our services today
- Date
- 22/05/2025