Optimol Instruments Revolutionises Tribological Testing
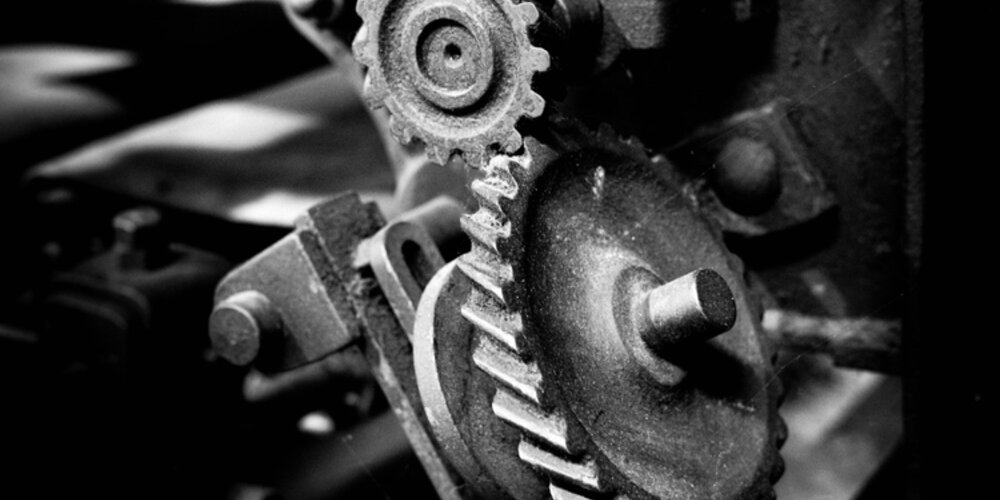
Optimol Instruments is transforming the field of tribological testing by offering precision test specimens that meet international standards, significantly reducing costs and error rates for companies.
In the demanding field of tribological testing, where accuracy and repeatability are top priorities, conventional testing methods have often fallen short, plagued by issues such as inaccurate results, high error rates, and unpredictable costs.
However, Optimol Instruments has embarked on a mission to revolutionise the field, offering innovative solutions that address these persistent challenges.
For over half a century, Optimol Instruments has been developing and manufacturing precision test specimens, playing a critical role in enhancing the reliability and efficiency of tribological testing.
“We understand the importance of high-quality reference test specimens,” said Managing Director of Optimol, Gregor Patzer. “Our experience and understanding of the details of tribological testing have prompted us to develop the perfect solution”.
One of the main issues with conventional tribological tests is their inherent unreliability. Multiple repeat tests are often necessary to obtain usable results, leading to significant time consumption and elevated operating costs.
The high risk of test failures and unnecessary material expenses further exacerbates the problem, creating a substantial financial burden for companies reliant on accurate testing.
Recognising these concerns, Optimol Instruments has developed reference test specimens that consistently adhere to the stringent specifications set out in international standards such as ISO, ASTM, and DIN.
This meticulous commitment to standards has resulted in a significant increase in test accuracy and a remarkable reduction in failure risk to less than 1%.
Optimol Instruments' offerings go beyond standardised test specimens. The company also provides customised solutions tailored to specific requirements, utilising a diverse range of materials including gear steel, stainless steel, aluminium, and ceramics.
Each test specimen is fully traceable and is accompanied by a certificate confirming compliance with all relevant specifications, reaching the highest level of quality and reliability.
The design of these specimens allows for multiple uses, drastically reducing the cost of consumables per test to less than 10 euros. This provides an enormous benefit for companies that depend on high test frequencies, allowing them to conduct extensive testing without additional costs.
By offering solutions that provide both accurate results and significant cost savings, Optimol Instruments is setting new standards in the field of tribology, revolutionising the way tribological testing is conducted.
Manufacturing engineering and mechanical failure services
If you require an expert to investigate a plant or machinery failure, then it’s vital that you select one with manufacturing-specific experience.
At Neale Consulting Engineers, our manufacturing-specific experience makes us the perfect partner for both proactive and reactive engineering and mechanical failure investigations.
We have a broad talent pool to draw upon. In addition to our origins in tribology, we have expert metallurgists, materials scientists, engineers, and others to assist in our investigations.
To learn more about our manufacturing engineering and mechanical failure services, contact us today.
Contact Neale Consulting Engineers today
- Date
- 04/04/2025